Introducing a New Class of Labour with Industry 4.0
November 16, 2018
There is a new shark circling in the waters of Dubai Marina. It is not the shark you were expecting, its name is WasteShark and it hunts pollution in the waters. WasteShark is a waterborne drone that eats up trash instead of living beings. It not only swallows floating waste and filters water but also collects water quality data. Measuring the temperate, air pressure and quality of the water is useful in collecting real-time data, allowing for a dynamic understanding of water quality. The WasteShark is an example of modern industry 4.0 in operation. It operates autonomously (which can be switched to manual operation via remote-control) and runs 24/7. Now with technological advances easing the work process, what does this mean for workers?
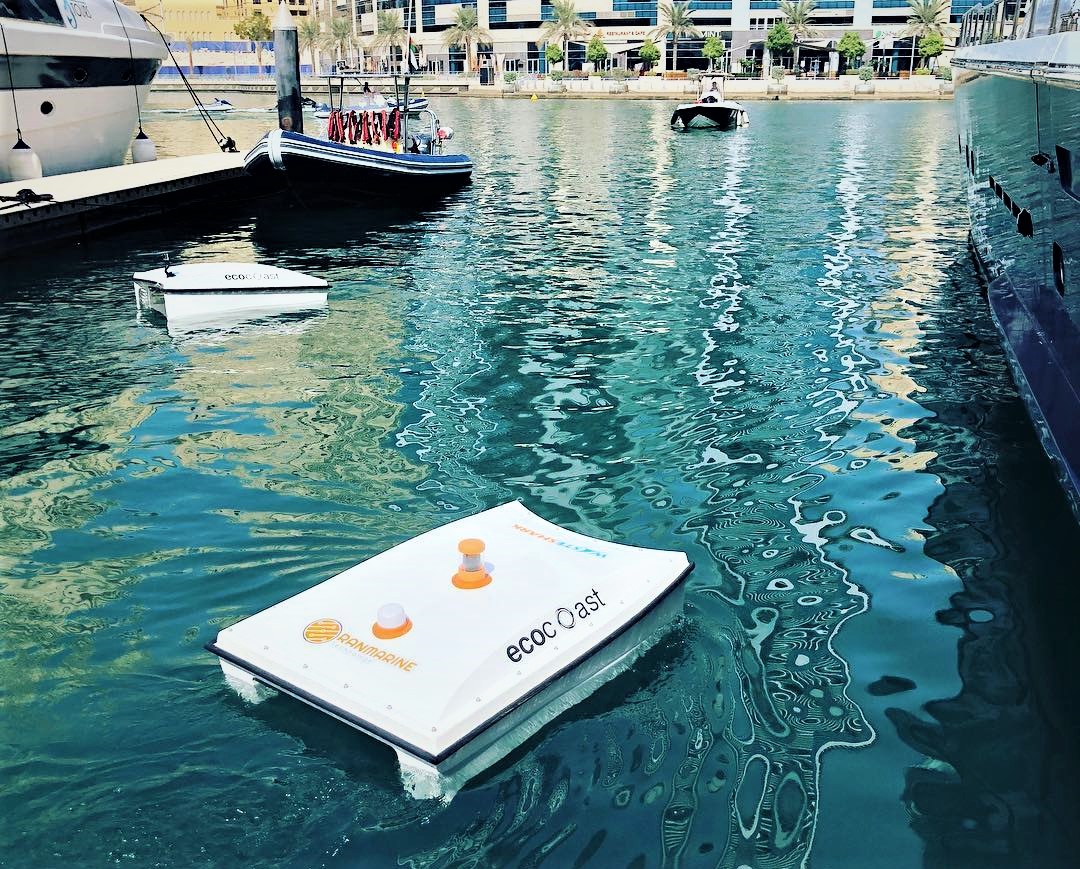
A great concern is raised in manufacturing, with jobs that will be redundant and jobs that could go unfilled due to a gap in skills. However, this is not the case as we have seen the impact of a relevant example – taxi booking application.
In Singapore, we have surely used one of these services, whether it is Uber or Grab. They have created a new economy that is shared, meaning that we are all a part of it, either contributing to it or gaining from it. It has created job opportunities for society with greater convenience and flexibility. Although facing the stumbling block of traditional taxi drivers losing customers, they soon overcame it by integrating themselves and leveraging on the system to benefit from it.
Similarly, the use of industry 4.0 will do the same for the manufacturing industry. It is going to create a new class of labour with new job opportunities. Instead of constantly monitoring screens 24 hours a day on a rotating shift, workers can engage on an on-demand basis and perform higher functions. In the case of WasteShark, workers need not go on site to physically remove the waste as these devices will do the job. This safeguards workers from biohazards and allows for an alteration of their job function, switching from manually clearing waste to controlling the device that will clear the waste.
Moving forward into industry 4.0, the skillset of jobs will undergo transition. The gap can be closed by acquiring new skills. It is easier to stay in the comfort zone of getting used to work processes but moving into change has a greater positive outcome that will increase productivity and efficiency. Change is necessary for us and we must be willing to take that extra step if we want to move into the new class of labour.
The jobs available today such as social media manager didn’t exist ten years ago. Networking is made easier and faster through social media, we are better connected globally in the public sphere thanks to technological advancements. The jobs we see today will unlikely be the same kind of jobs we will see in the next decade. The functions we will perform will be of a higher level.
Singapore is already working educating the young labour force as early as kindergarten! An integrated STEM education is being introduced into kindergarten curriculums up to higher learning institutions. This generation has already integrated into the digital world, and those are the jobs that will be created in the manufacturing industry where they will handle physical assets in a digital manner.
Industry 4.0 is here to improve working conditions, it is a gateway to a new class of labour. Are you ready for change?
Topic(s): Learning & Development, Productivity
Delivering Effective Presentations at LSBF
Recruitment Practices Tripartite Standard by TAFEP